Imagine a situation in which your vendor had a breakdown and cannot deliver your goods for sometime. What will be your approach to this situation?
Are you going to delay your customer delivery due to these issues?
Are you going to spend more and fetch goods from some other vendors? What about the old vendor delivering the goods later?
These dangling questions are very common in a supply chain business, where we cannot wait for such unforeseen events to plan our delivery. This is where a safety stock comes into the picture.
Let’s take an example of the cloth industry, if you are an industry which makes winter jackets and your vendors is not able to deliver wool for the jacket, will you wait for him and delay your production? Or use your buffer stock to get the jackets ready before the winter starts?
Many companies have their own model to follow when it comes to Safety stock and its maintenance. Let’s understand more about safety stock and its benefits.
What is safety stock?
“Safety Stock” as the words suggests, is a certain amount of buffer inventory kept by a business, to prevent any unexpected events like sudden spike in demand or supply from vendors and other suppliers.
With the growing rate of technology and changing customer trends, many companies are moving towards ( Just-in-time) JIT inventory system. With JIT technologies, many companies have been ordering small amounts of inventory on a regular basis.
The concept of Just-in-time inventory is that, companies order inventories which are enough for a week or two, so that they can get rid of stock storage limitations. Inventory in this model is delivered sometimes as often as a few times a day, which saves the cost of storing the inventory for the future. Many business giants like Apple use this JIT model to save the cost on stock storage. As mentioned by Tim Cook, CEO of Apple, “Inventory is fundamentally evil. You kind of want to manage it like you’re in the dairy business. If it gets past its freshness date, you have a problem.”
But, not all companies can follow just-in-time methodologies because they don’t have a regular mode of inventory delivery. Most the business which aren’t close to the supplier or the have difficulty in procuring the raw materials, follow the model of Safety Inventory System.
In this Safety stock system, companies buy more inventories than they can use and store it for future usage. This excess inventory is called their safety stock. This storage methodology ensures that the company won’t run out of their raw material and spare parts during a busy season. In other words, companies overstock their product so that they don’t have any “out of stock” situation in the peak delivery time.
In today’s highly competitive global economy, inventory has become the focus of improvement for many companies to keep their customer satisfaction level high. Buffer stock is a good idea for customer satisfaction, but is very susceptible to losses for the company.
Stock safety is a good tool to always keep our customers happy as stores never run out of stock for their favourite product but, it can be a costly affair for most of the growing businesses with less infrastructure and restricted money inflow. Therefore, every inventory managing business needs an excellent inventory management software to determine how much safety stock is required to lower the risks of unexpected stock-out and also suffice the product demand.
Reasons for keeping Safety Stock
Safety stock essentially seeks its application in a make-to-stock manufacturing planning, which is utilized when manufacturing lead times must go along with clients preferences and needs in accordance with the cost and timing. The foremost purpose of safety stock is to take up the volatility in customer preferences and requirements. The foundation of safety stock performs to secure against stockouts arising from fluctuations and upward trends in customer demand.
Safety stock serves as a protective measure against potential stock outs resulted due to erroneous planning and scheduling. Specifically, perishable goods possessing a limited shelf life, which are food and beverages, tend to be at risk of spoilage if kept as a safety stock for elevated periods. Utilizing advanced technology, fabricating closer collaborations with suppliers, and evaluating forecasting accuracy are techniques that can reduce the reliance on safety stock.
Importance of Safety stock
- Safeguarding Against Demand Surges: Safety stock delivers a protection against sudden increase in demand and erroneous market forecasts, which are common during busy seasons or festive periods. It assures that a company will continuously fulfill orders without exhausting its inventory of particular items.
- Buffering Against Longer Lead Times: Even though suppliers are mostly dependable in delivering products on a committed schedule, unpredicted disruptions can take place. Aspects such as production delays, congestion at the supplier’s side, or any sort of shipping delays caused due to unfavorable weather can result in products arriving later than anticipated. Safety stock delivers to be as a defense against potential stockouts in such situations.
- Protection Against Price Fluctuations: Market unpredictability can result in sudden expense increases for goods. Such may arise from aspects such as raw material shortages, elevated demand, or the arrival of new competitors. Managing adequate safety stock during unfavorable circumstances supports avert the requirements to purchase inventory at heightened prices.
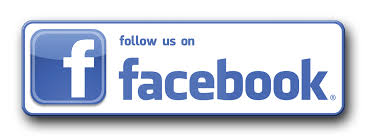
Why do we need safety cost?
Demand and sales chain is a variable entity, affected by seasonal effects, one-off ‘shock’ events, new customers being converted, old customers leaving, customer demand changes or flawed forecasting. Due to these numerous uncertainties in various business models, having a good amount of safety stock helps to keep our customers satisfied with on time delivery.
Demand forecasting is one of the measures to understand the trends of your business model, products demand and supply chain, which will help to forecast the approximate amount of inventory for current and future product delivery. Best we can do is to have demand forecasting methods to be as accurate as possible, but ultimately these are just predictions. As supply cycle and supplier have many regular issues which might arise at real time, 100% guarantee of the stock prediction amount is nearly impossible.
Many businesses rely on on-the-spot inventory management and don’t spend on safety stock which may cause them some of the issues like –
- Loss of revenue
- Lost customers
- Loss in market share
Taking the time to use the safety stock formula not only saves you from these costs but also increases revenue and higher customer service level.
How to calculate Safety stock inventory?
There are many formulas in the market which can be used to calculate the most accurate amount of safety stock that should be kept in our warehouse based on various factors in a particular business.
Here’s the formula you can use if you’re just starting out:
(Max Daily Sales x Max Lead Time in Days) – (Average Daily Sales x Average Lead Time in Days) = Safety Stock Inventory
Lead Time – time to sell your current products.
However, we should keep in mind that “One size fits all” approach does not apply completely for the safety stock inventory as its dependent on many important factors, such as service level, forecast accuracy and lead time variability. Based on these variable components, we need to adjust our safety stock levels accordingly.
What are the Benefits of Safety Stock Inventory?
1. Avoid delay in manufacturing
Different business models have different levels of fluctuation in both demand and supply values. Using safety stock should be directly proportionate with the fluctuation rate, i.e the greater the potential fluctuation, the greater the level of safety stock should be. Usually, fluctuation rate is the major reason of manufacturing delays. Once we understand our delays and the predictable reasons around it, we should estimate our stock level as per these fluctuations.
If we have these unpredictable covered with safety stocks, we can continue to manufacture our good irrespective of product delivery uncertainty and our final products will have no issues in completing. With this approach, we can give on time delivery to our customers and improve our customer satisfaction level.
2. Customer satisfaction
Customer experience and overall satisfaction level have a large impact on the success of a business. In today’s world of social media and group chats mode, one unhappy customer can cause loss of many potential clients for the retail business. Hence, customer centricity plays a very important role in maintaining a good inflow of revenue for the business.
Safety stocks are one of the major contributors of keeping our customers happy by providing them a smooth supply chain mechanism. Stocks in the warehouse seem to no way related to end customer, but if we see closing these safety stocks are sometimes the main reason of providing on time delivery to customers and keep them coming back to us for business.
Safety stocks will overrule the various restrictions businesses have related to vendor deliveries, stock damages and many more, which can delay customer product delivery and cause client dissatisfaction for the business.
3. Cost
In most of cases, the retail business models, inventory holding cost will vary between 20-40% of the cost of the stocked merchandise. These additional stock safety cost sometime doesn’t endup for a day or two but may extend upto payoff for a complete year.
Due to the high rate of safety stock management, many startups and small scale companies trade-off between stock safety and minimising inventory storage costs.
Read More – SalesBabu Inventory Management Software for Inventory Management for SME
But if we see on the longer run, every unsatisfied customer who is planning to change his service vendor due to delay in delivery, can cost much more than the safety stock storage cost.
If we plan our inventory storage appropriately with a good inventory management software, we can strike a balance between storing safety stock with minimum investment and also keep our customers happy with on time delivery.
Read More – Reduce Operational Cost With Inventory Management System
4. Wastage
Many small scale companies might claim that safety stock is an additional wastage of business revenue, but if we research well, we will understand that in many cases delay in delivery from vendors leave a lot of raw material wasted and unused. These raw materials often get destroyed due to delay in production and cause wastage of items. With an appropriate amount of safety stocks, we can not only complete our deliveries on time but also save a lot of materials from being wasted due to decay and theft.
Safety stocks in all are the best way to save our products from getting wasted and providing on time delivery.
Read More – Efficient Inventory Management System
Conclusion
From a broader perspective, there is a thin line between safety stocks and excess-stock. Hence to determine the adequate amount needed for our product consumption and avoiding the excess stock, we need a good analytical & report generating tool which can help our business in effective demand forecasting.With an efficient stock management tool like SalesBabuCRM, can determine the balance between the level of safety stock needed for providing an efficient sales cycle for our business. If we can gaze our business strategies properly, good sales would keep on increasing with reduced storage cost for inventory.